Through its proprietary technology, Monolith has innovated the thermal plasma process, a form of pyrolysis which harnesses electricity to create a superheated plasma that cracks hydrocarbon molecules into basic elements, carbon and hydrogen. This process significantly reduces life-cycle carbon emissions from both carbon black and hydrogen production while reducing America's dependence on foreign imports.
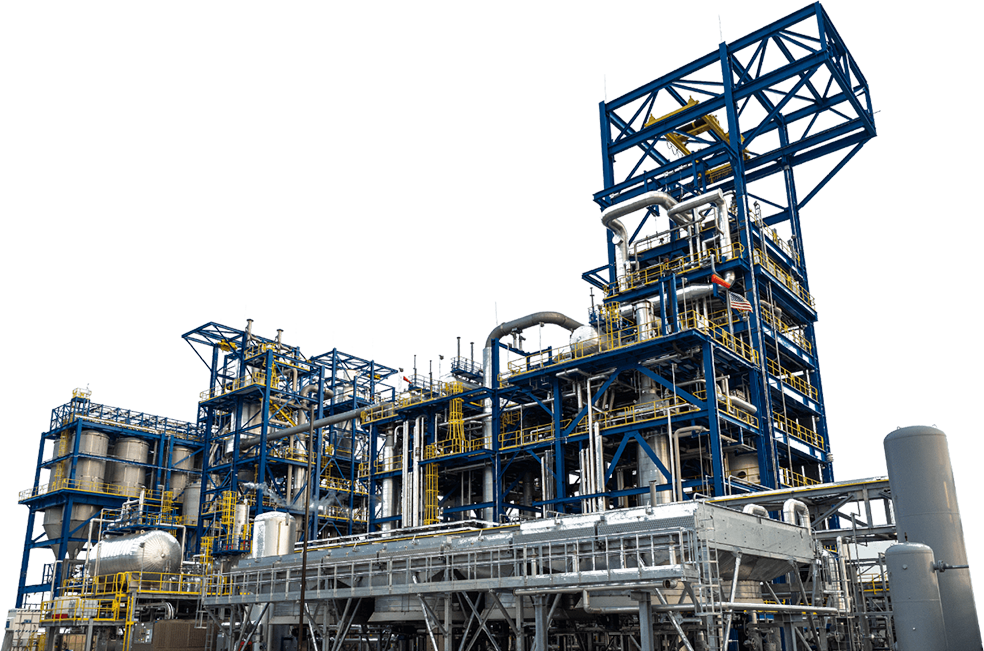
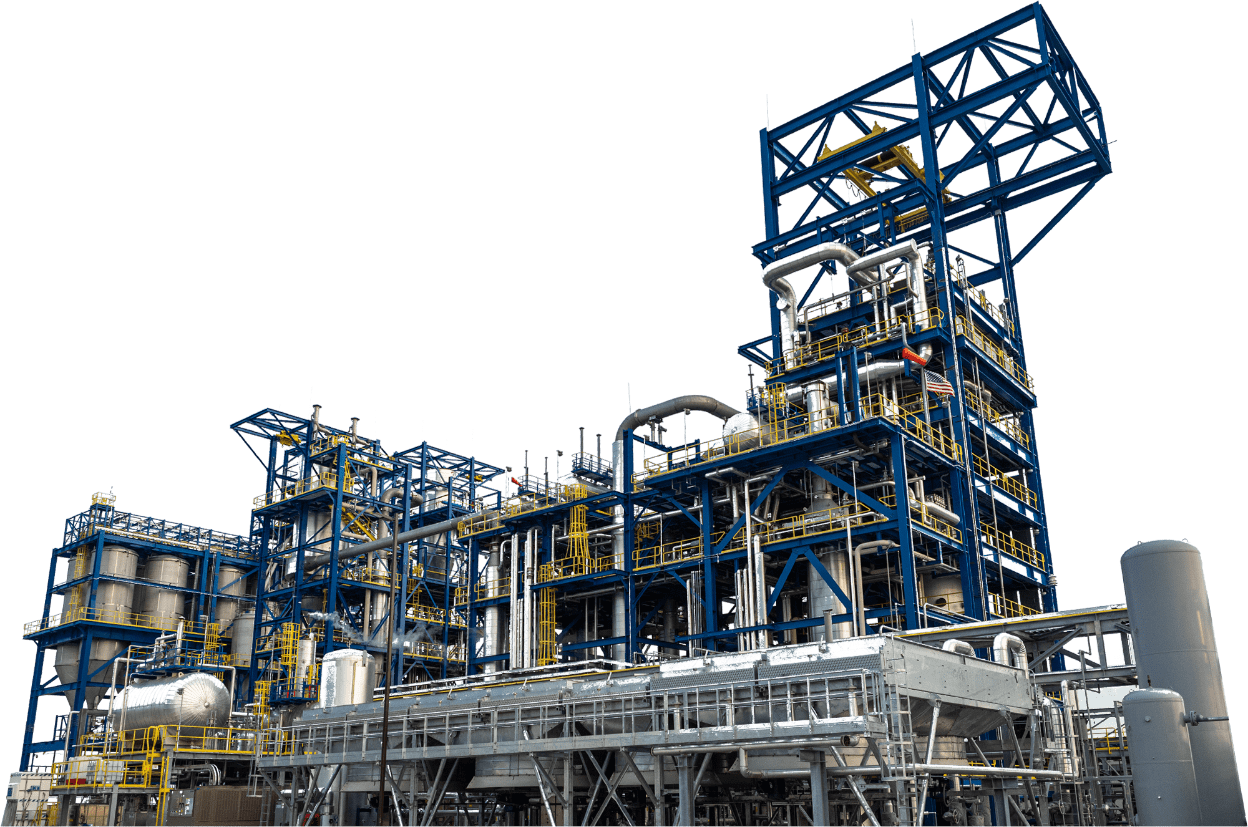
The Monolith Process
The Monolith Process
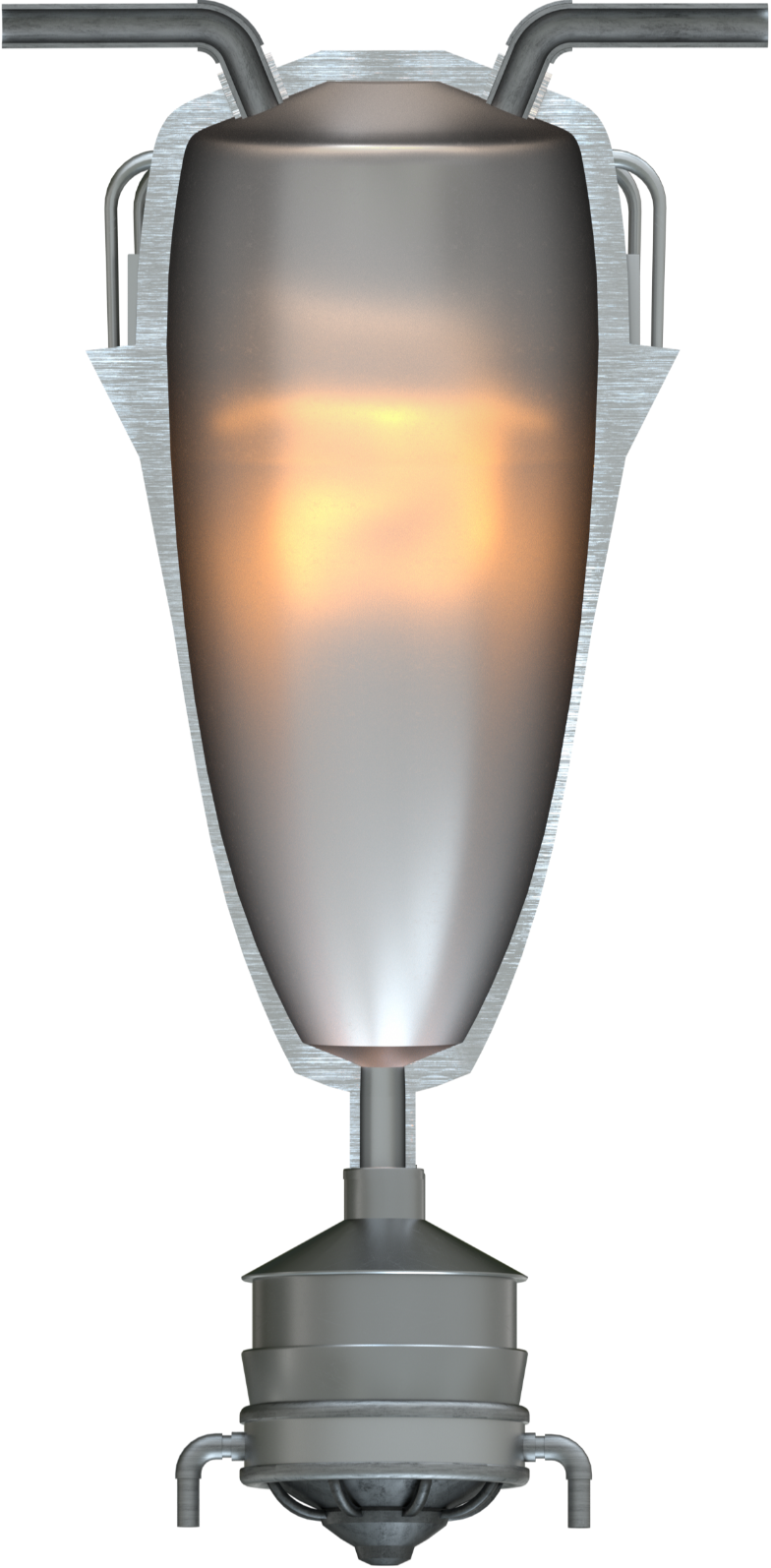
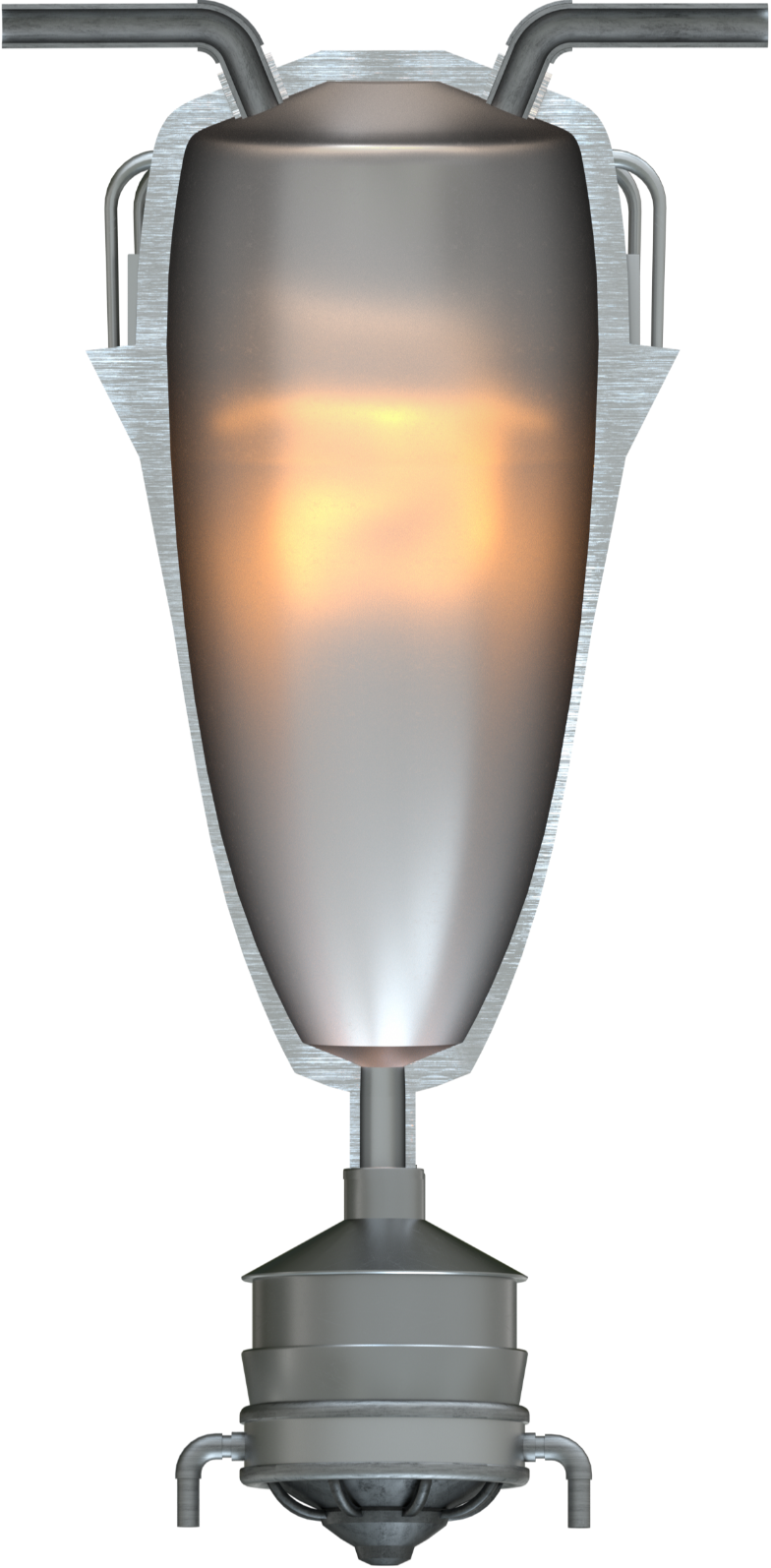
Hydrocarbon feedstock enters here.
A process gas can be added to help heat the hydrocarbons.
The hydrocarbon is superheated by electricity. This is combustion-free and CO2-free.
The heat breaks the bonds between the hydrogen and carbon in the hydrocarbon molecule.
The pairs of hydrogen atoms and carbon atoms move through the chamber and exit separately.
From here, the hydrogen is directed to end-users. The carbon is further processed into multiple grades of high-performance carbon blacks.
The plasma advantage
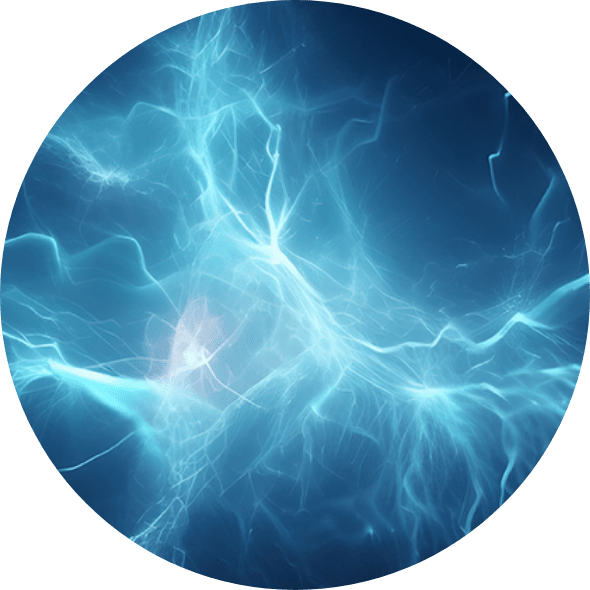
Combustion-free
No oxygen is present inside the plasma reactor. Instead, clean electricity essentially creates a constant stream of lightning that superheats the hydrocarbon molecule and breaks it apart. There is no flame and no combustion, unlike when oil is burned in the conventional furnace process to make carbon black.
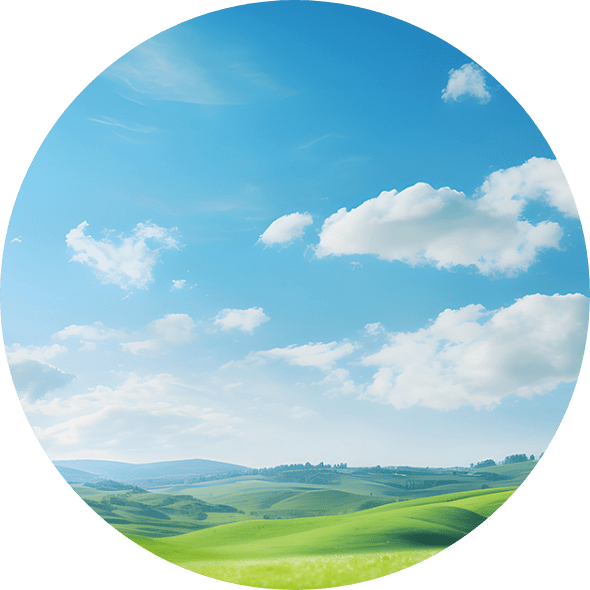
Market Driven
Monolith's innovation represents a resurgence in American-made carbon black that reduces our reliance on imports while meeting customer demands for high-performing carbon black.
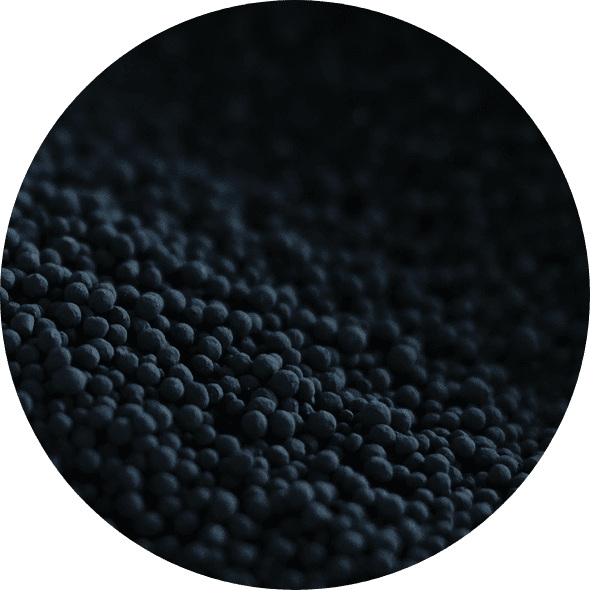
Greater yield
The plasma process is even more efficient — delivering a yield of up to 95 percent, compared to conventional manufacturing’s 55 to 60 percent.